
Concrete Overview
Forget the SCMs you thought you knew.
Our novel technology platform unlocks new advances in strength and durability for cement replacements. By permanently storing CO2 in industrial byproducts and natural materials—from coal plants, steel mills, glass manufacturing, mine sites, and more—we are improving performance and lower emissions of concrete. Our improvements in performance are third-party validated, too.
As the concrete industry strives for decarbonization, many have embraced supplementary cementitious materials (SCMs)—an alternative to traditional portland cement that can meet concrete performance requirements while reducing CO2 emissions. However, SCMs are niche today, can only achieve low blend rates, and are being imported from overseas as supply becomes scarce in North America.
Our technology enables the reduction of clinker in cement, and cement in concrete, providing a solution to both cement producers and ready mix concrete producers. We’ve fundamentally changed the way we create SCMs, driving three benefits (below) from a single process and opening up a massive market for cement replacement.
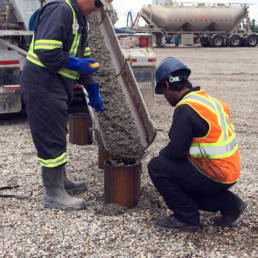
Carbon Upcycling
Our Benefits
We reduce in 2 ways. 1) Our technology locks CO2 permanently inside SCMs and 2) Reduces the amount of cement required in concrete. We often work with cement and concrete producers to utilize the CO2 they already have onsite, which is generally a low purity CO2 source. For some materials, we can reach a sequestration rate up to 15%. We also reduce second order CO2 emissions by removing the need to import expensive SCM feedstocks from overseas; we use local industrial waste and natural materials instead. Carbon Upcycling’s SCMs decrease the amount of cement used in the production of concrete by up to 20%.
Our technology is unique in its ability to utilize onsite CO2 emissions and industrial wastes or natural materials found in almost any region of the globe. This allows us to mitigate material transportation costs and seamlessly integrate into local ecosystems. And of course, by using local feedstocks we create a more resilient supply chain and building infrastructure wherever our technology is used.
By supercharging the reactivity of industrial byproducts and natural materials we increase CO2 utilization and create an SCM that is superior to all other SCMs. Our SCMs have been proven by third parties to improve concrete durability by 60% and strength by up to 40%. Now we can build bridges and cities that are even safer, and work to save the planet at the same time.
How We Integrate
Deploying our Technology
Our catalytic reactor installs onsite at cement production facilities and ready mix facilities. Running in parallel to your existing processes, our production step can harness CO2 you already have onsite and put it to productive use while still meeting or exceeding your mix performance requirements.
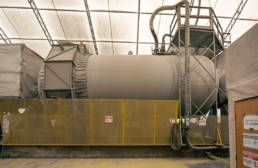
Take Action
Lets Talk!
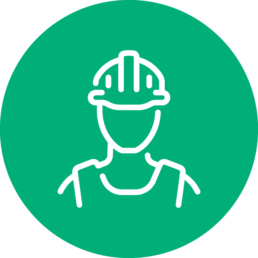
For Cement Producers
Deploying our technology is swift, and we take on much of the installation and operating risks. Expand your use of SCMs while lowering the cost to create them at the same time.
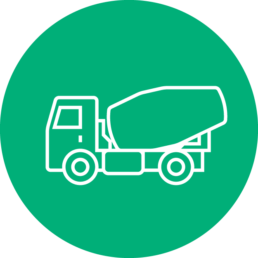
For Ready Mix Producers
Go way beyond the current standard for sequestering CO2 in your mix, and improve performance at the same time.
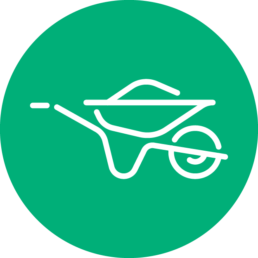
For Feedstock Providers
We’re opening a whole new class of feedstocks for cement and concrete production. Find out if your materials now have a new set of customers because of our technology.
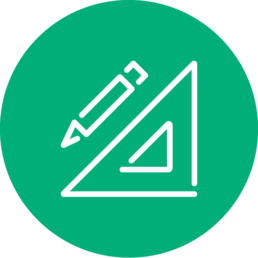
For Architects & Builders
Cement and concrete are major contributors to embedded emissions in buildings. Get our spec sheets and start integrating our customer’s products in your building plans.